El Mantenimiento Neumático es un aspecto fundamental en la operación eficiente de equipos industriales que utilizan aire comprimido para su funcionamiento. En sectores exigentes como el alimentario, farmacéutico o plástico, la continuidad operativa depende de la confiabilidad de estos sistemas neumáticos. Sin un enfoque técnico adecuado, las fallas pueden derivar en paradas costosas, mermas productivas y riesgos innecesarios para la planta.
La confiabilidad industrial no se limita a la calidad de los componentes instalados, sino que requiere una gestión sistemática del mantenimiento preventivo. Equipos sometidos a condiciones de presión, humedad o agentes contaminantes deben ser evaluados periódicamente. Un diagnóstico técnico a tiempo permite identificar fugas, pérdidas de fuerza o consumos energéticos elevados que, sin ser evidentes, afectan la eficiencia y reducen la vida útil de los sistemas neumáticos.
Muchas empresas subestiman el impacto de un mantenimiento deficiente en la tecnología neumática. Fallos en actuadores, líneas de distribución o válvulas mal calibradas pueden comprometer la seguridad operativa y disminuir la precisión en procesos automatizados. Esto es especialmente crítico en industrias con altos estándares de control, como la cosmética o la farmacéutica, donde cualquier desviación puede representar un incumplimiento normativo y pérdidas económicas significativas.
Desde Representaciones Industriales RDV, los invitamos a continuar leyendo este artículo y descubrir cómo una estrategia de mantenimiento planificada puede optimizar recursos, proteger sus activos y asegurar una operación confiable, limpia y eficiente.
Conozca más de nuestras soluciones para la industria. Tal vez le interese leer: Automatización Neumática, Soluciones para Fábricas del Futuro.
Table of Contents
Fundamentos técnicos de los sistemas neumáticos
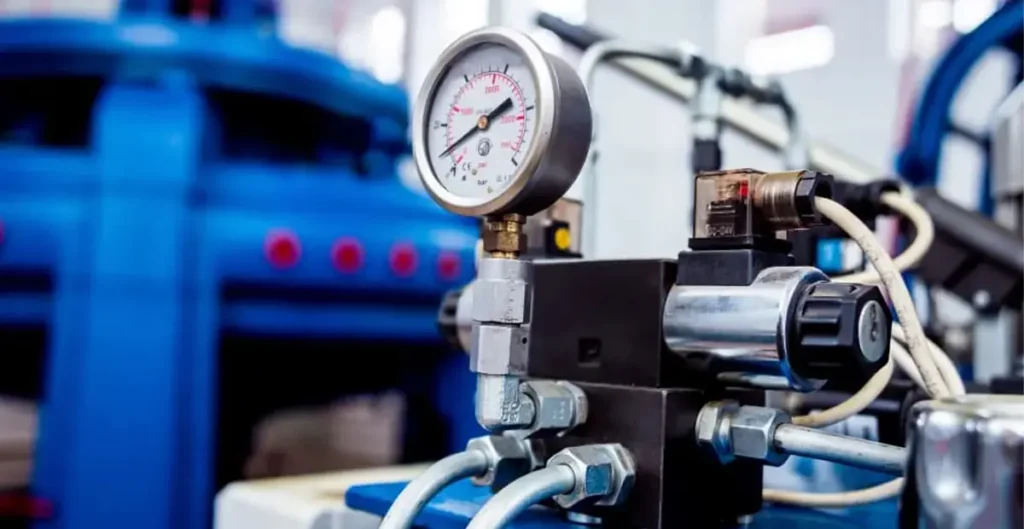
Los sistemas neumáticos industriales son conjuntos diseñados para transformar la energía del aire comprimido en trabajo mecánico, mediante componentes que permiten controlar con precisión la fuerza, el movimiento y la velocidad de procesos automatizados. Su funcionamiento se basa en el principio de la dinámica de gases, donde el aire comprimido, al expandirse, transfiere energía útil a actuadores o herramientas.
Componentes clave del sistema neumático
Un sistema neumático completo se compone de cinco bloques principales:
- Generación: a través de compresores que elevan la presión del aire ambiente a niveles operativos (6–8 bar normalmente).
- Tratamiento: el aire pasa por filtros, reguladores y lubricadores (FRL) que eliminan impurezas, estabilizan la presión y, en algunos casos, lubrican para reducir el desgaste de componentes móviles.
- Distribución: mediante tuberías, mangueras y acoples, el aire comprimido es transportado hacia las zonas de trabajo. La calidad de estos elementos afecta directamente la eficiencia del sistema.
- Control: se realiza mediante válvulas direccionales, reguladoras de caudal y electroválvulas, que gestionan la trayectoria, velocidad y presión del aire.
- Actuación: aquí el aire realiza el trabajo, moviendo cilindros, pinzas, motores neumáticos u otros actuadores lineales o rotativos.
Cada uno de estos elementos debe seleccionarse e integrarse según las condiciones de operación específicas: tipo de proceso, carga, velocidad requerida, entorno físico (temperatura, humedad, polvo) y grado de automatización.
Tipologías de mantenimiento neumático
Puede abordarse desde tres enfoques complementarios: correctivo, preventivo y predictivo. El correctivo se activa tras una falla, siendo el más costoso por su carácter reactivo y la interrupción inesperada del proceso. Si bien es inevitable en algunos casos, depender únicamente de esta estrategia es una mala práctica técnica, especialmente en plantas de alta criticidad operativa.
- El mantenimiento preventivo se basa en rutinas calendarizadas: inspección de mangueras, limpieza de filtros, verificación de estanqueidad, lubricación de componentes y ajuste de presiones. Su objetivo es anticiparse al desgaste natural por uso, considerando los ciclos de trabajo y las condiciones ambientales. En ambientes con alta presencia de polvo, humedad o agentes corrosivos, estas intervenciones deben ajustarse con mayor frecuencia.
- El enfoque predictivo, por su parte, se apoya en el análisis de variables físicas para anticipar fallas: vibraciones en actuadores, caídas de presión en línea, temperatura en válvulas o variaciones en el consumo de aire. Herramientas como sensores IoT, monitoreo remoto y software de análisis permiten detectar patrones anómalos antes de que el sistema colapse. Esta visión técnica integrada posiciona al mantenimiento como un generador de valor, no como un costo.
Señales de desgaste o mal funcionamiento
Detectar oportunamente los signos de desgaste en componentes neumáticos es vital para evitar daños mayores. Una pérdida progresiva de presión, ciclos más lentos o movimientos intermitentes suelen ser indicios de fugas o deterioro interno en actuadores. Del mismo modo, ruidos inusuales o golpes secos pueden revelar desalineaciones, obstrucciones o falta de lubricación adecuada.
Otro signo frecuente es el aumento en el consumo de aire comprimido, que muchas veces no se relaciona con una mayor producción, sino con microfugas en conexiones o mangueras degradadas. Este exceso puede pasar desapercibido en sistemas grandes, pero impacta directamente en la eficiencia energética de la planta y en la vida útil del compresor.
En instalaciones con procesos regulados, como la farmacéutica o alimentaria, una válvula que no actúa con precisión puede afectar la dosificación de ingredientes o el envasado, comprometiendo la calidad final del producto. Por ello, es indispensable capacitar al personal para reconocer estos síntomas y actuar preventivamente, integrando inspección visual con pruebas funcionales y registros técnicos de cada intervención.
Consecuencias de no realizar mantenimiento oportuno
Omitir o postergar el mantenimiento de sistemas neumáticos genera una serie de consecuencias técnicas y económicas que comprometen la continuidad operativa, la eficiencia energética y la seguridad industrial. A continuación, se presentan los impactos más críticos:
🔧 Consecuencias operativas
- Paradas no programadas de producción: una falla repentina en un actuador o válvula crítica puede detener líneas completas, generando pérdidas por hora difíciles de recuperar.
- Desbalance en los ciclos de producción: presión inestable o fallos intermitentes provocan velocidades irregulares y pérdida de sincronización entre equipos automatizados.
- Caída en la precisión de dosificación o manipulación: en sectores como farmacéutica o alimentos, una válvula fuera de calibración puede afectar directamente la calidad del producto final.
⚙️ Consecuencias técnicas
- Acelerado desgaste de componentes: el funcionamiento continuo de actuadores con fricción elevada o sin lubricación incrementa el deterioro y reduce la vida útil de las piezas.
Fugas en líneas de distribución: una manguera fatigada o un acople deteriorado provocan pérdidas constantes de aire comprimido, afectando la presión de trabajo del sistema. - Contaminación del aire comprimido: filtros saturados o sistemas de tratamiento ignorados permiten el paso de humedad, partículas o aceite, dañando válvulas y actuadores.
⚠️ Consecuencias en seguridad y normativas
- Riesgos para operarios: sobrepresiones, golpes de ariete o válvulas defectuosas pueden provocar movimientos bruscos o fugas violentas, comprometiendo la seguridad del personal.
- No conformidad normativa: en industrias reguladas por estándares GMP, ISO 22000 o FDA, un sistema fuera de especificación puede significar el rechazo de lotes enteros.
- Falta de trazabilidad técnica: sin registros de mantenimiento, resulta imposible identificar causas raíz o justificar el estado técnico del sistema ante auditorías.
💸 Consecuencias económicas
- Incremento del consumo energético: un sistema con fugas o desbalanceado obliga al compresor a trabajar más, elevando los costos eléctricos de forma sostenida.
- Mayores costos de reparación: reemplazar componentes dañados por uso prolongado sin revisión es más costoso que intervenir preventivamente.
Impacto en la rentabilidad global: cada hora de inactividad o cada lote defectuoso se traduce en pérdidas directas en la rentabilidad operativa de la empresa.
Buenas prácticas para una estrategia de mantenimiento eficiente
Una estrategia efectiva de mantenimiento neumático comienza con una planificación basada en datos técnicos reales. Esto incluye definir cronogramas periódicos según las horas de operación, establecer checklists estandarizados para inspecciones y mantener una trazabilidad completa de las intervenciones. El uso de software de gestión de mantenimiento (CMMS) permite organizar y documentar todas las acciones, facilitando la toma de decisiones.
Implementar indicadores como el índice de fallas por componente, el tiempo medio entre fallas (MTBF) y el tiempo medio de reparación (MTTR) ayuda a evaluar el estado de los equipos y la efectividad del mantenimiento. Estos KPI permiten priorizar acciones correctivas y justificar inversiones en actualización de componentes o rediseños de sistemas obsoletos.
La capacitación técnica del personal es igualmente crucial. Un operario capaz de interpretar variaciones de presión o identificar una válvula deteriorada puede prevenir daños mayores con una acción rápida. Finalmente, mantener un inventario básico de repuestos críticos garantiza respuesta inmediata ante emergencias. Estas prácticas integradas permiten al área de mantenimiento pasar de ser reactiva a ser un verdadero pilar de la productividad industrial.
Cómo Representaciones Industriales RDV puede ser su aliado
En Representaciones Industriales RDV entendemos que el rendimiento de su sistema neumático depende tanto de la calidad de los componentes como del conocimiento técnico con el que se gestionan. Por eso, no solo ofrecemos productos como mangueras, acoples, sistemas neumáticos, instrumentación o cortinas termoplásticas, sino que también brindamos asesoría especializada para cada aplicación.
Nuestros más de 30 años en el sector industrial colombiano nos permiten entender las necesidades particulares de industrias como la alimentaria, farmacéutica, cosmética o plástica. A través de soluciones personalizadas, apoyamos a nuestros clientes desde la selección adecuada de materiales hasta la instalación y puesta en marcha. Además, contamos con un portafolio de empaques industriales, plásticos de ingeniería y línea neumática que complementan integralmente cualquier sistema.
Ya sea que necesite mejorar el rendimiento de su sistema actual o implementar una solución desde cero, nuestro equipo técnico está preparado para acompañarlo. Nos enfocamos en maximizar la eficiencia, reducir tiempos muertos y extender la vida útil de cada componente neumático.